2025 Autor: Howard Calhoun | [email protected]. Naposledy zmenené: 2025-06-01 07:15
Vedúci akéhokoľvek podniku, bez ohľadu na oblasť činnosti, sníva o tom, že zisky rastú a výrobné náklady zostanú nezmenené. K dosiahnutiu tohto výsledku pomáha systém „5S“vo výrobe (v anglickej verzii 5S), ktorý je založený len na racionálnom využívaní vnútorných rezerv.
Tento systém nebol vytvorený úplne od začiatku. Niečo podobné koncom 19. storočia navrhol Američan Frederick Taylor. V Rusku to urobil vedec, revolucionár, filozof a ideológ A. A. Bogdanov, ktorý v roku 1911 vydal knihu o princípoch vedeckého manažmentu. Na základe ustanovení v ňom uvedených ZSSR zaviedol NOT, teda vedeckú organizáciu práce. Ale najdokonalejší bol systém 5C navrhnutý japonským inžinierom Taiichi Ohno a ním predstavený v závode Toyota Motor vo výrobe. Čo to je a prečo sa japonský systém stal takým populárnym?
Faktom je, že je založený na jednoduchom princípe, ktorý si nevyžaduje náklady. Spočíva vďalší - každý zamestnanec, od upratovačky až po riaditeľa, by mal čo najviac optimalizovať svoj podiel na celkovom pracovnom toku. To vedie k zvýšeniu zisku výroby ako celku a k zvýšeniu príjmov všetkých jej zamestnancov. Teraz štafetu zavedenia systému „5C“prevzali podniky po celom svete vrátane Ruska. V tomto článku sa pokúsime presvedčiť skeptikov, že japonské know-how skutočne funguje, a to úplne v akejkoľvek oblasti činnosti.
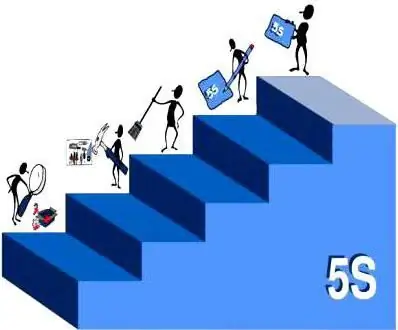
Systém „5C“vo výrobe, čo to je
International 5S znamená päť krokov ("krok" v angličtine step). Niektorí ekonómovia a propagátori nového prístupu k práci vysvetľujú názov piatimi japonskými postulátmi, ktoré sú dôsledne implementované v systéme 5S: seiri, seiton, seiso, seiketsu a shitsuke. Pre nás sú bližšie a zrozumiteľnejšie naše rodné „5C“- päť na seba nadväzujúcich krokov, ktoré je potrebné absolvovať, aby sme dosiahli prosperitu našej výroby. Toto je:
1. Zoradiť.
2. Udržiavanie objednávky.
3. Udržiavanie čistoty.
4. Štandardizácia.
5. Zlepšenie.
Ako vidíte, systém „5C“nevyžaduje pri výrobe nič nadprirodzené. Možno práve preto sa k nej stále možno stretnúť s nedôverou a ľahkomyseľným prístupom.
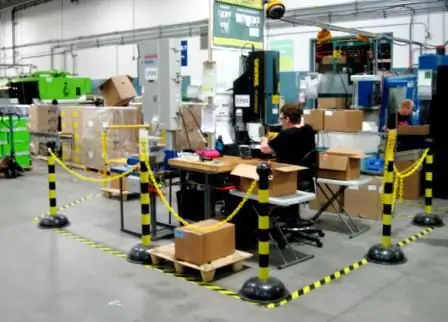
Fázy vytvárania systému
Múdry Japonec Taiichi Ohno, ktorému sa vďaka zavedeniu jeho metód v závode Toyota podarilo povzniesť zinžinier na generálneho riaditeľa, si všimol, koľko strát vzniká v dôsledku rôznych nezrovnalostí a prekrytí. Napríklad niektoré malé skrutky neboli včas nasadené na dopravník a v dôsledku toho sa zastavila celá výroba. Alebo naopak, diely boli dodávané s maržou, ukázali sa ako nadbytočné a v dôsledku toho ich jeden zo zamestnancov musel odviezť späť do skladu, čo znamená strácať čas prázdnou prácou. Taiichi Ohno vyvinul koncept, ktorý nazval „práve včas“. To znamená, že na dopravník bolo teraz doručených presne toľko dielov, koľko bolo potrebné.
Dajú sa uviesť aj iné príklady. Systém „5S“vo výrobe obsahoval aj koncept „kanban“, čo v japončine znamená „reklamný nápis“. Taiichi Ohno navrhol pripevniť takzvaný „kanban“štítok na každý diel alebo každý nástroj, v ktorom boli uvedené všetky potrebné informácie o diele alebo nástroji. V podstate to platí na čokoľvek. Napríklad na tovar, lieky, šanóny v kancelárii. Tretím konceptom, na ktorom je systém 5S vo výrobe založený, je koncept „kaizen“, čo znamená neustále zlepšovanie. Boli koncipované aj iné koncepty, ktoré boli vhodné len pre vysoko špecializované výrobné procesy. V tomto článku ich nebudeme brať do úvahy. Výsledkom všetkých v praxi overených inovácií bolo vytvorených 5 krokov, ktoré sú aplikovateľné na akúkoľvek výrobu. Poďme si ich podrobne analyzovať.
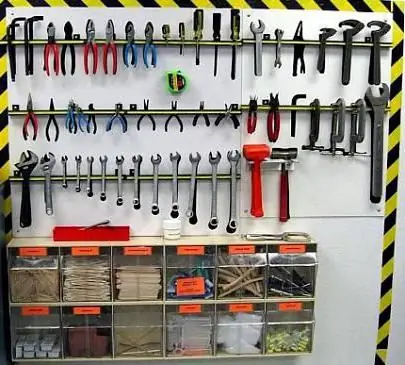
Sorting
Mnohí z nás majú na svojich počítačoch položky, ktoré vv podstate netreba. Napríklad staré formuláre, nepoužívané súbory, návrhy výpočtov, obrúsok, na ktorom bola šálka kávy. A medzi týmto chaosom môžu byť potrebné súbory alebo dokumenty. Základné princípy systému „5S“zahŕňajú optimalizáciu vášho pracovného toku, teda zabezpečenie toho, aby sa nestrácal čas hľadaním tých správnych vecí medzi troskami nepotrebného. Toto je triedenie. To znamená, že na pracovisku (v blízkosti stroja, na stole, v dielni - kdekoľvek) sú všetky položky rozložené na dve hromady - potrebné a nepotrebné, ktoré sa musia zlikvidovať. Ďalej sa všetko, čo potrebujete, rozloží do nasledujúcich kôp: „používané často a neustále“, „používané zriedka“, „takmer nepoužívané“. Týmto je triedenie dokončené.
Udržiavanie objednávky
Ak položky len rozoberiete, nebude to mať zmysel. Tieto predmety (náradie, dokumenty) je potrebné usporiadať v takom poradí, aby to, čo sa neustále a často používa, bolo na očiach, prípadne aby sa to dalo rýchlo vziať a jednoducho vrátiť späť. To, čo sa používa málo, sa dá poslať niekam do krabice, ale treba na to pripevniť kanban tag, aby sa to po chvíli dalo ľahko a presne nájsť. Ako vidíte, systém 5S na pracovisku začína najjednoduchšími krokmi, no v skutočnosti sa ukazuje ako veľmi efektívny. A okrem toho zlepšuje náladu a chuť do práce.
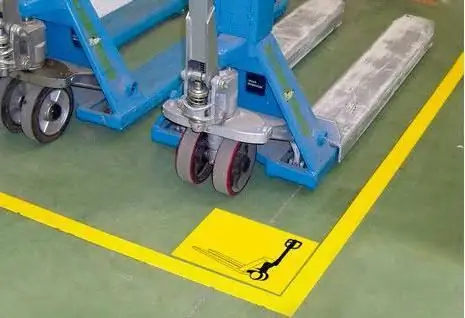
Udržiavanie čistoty
Tento tretí krok je pre mnohých najlogickejší. Od detstva nás učia byť čistí. Navo výrobe je tiež potrebné a čisté by mali byť nielen stoly kancelárskych pracovníkov či skrine v stravovacích zariadeniach, ale aj stroje, technické miestnosti upratovačiek. V Japonsku sa zamestnanci o svoje pracoviská vzorne starajú, upratujú sa trikrát denne - ráno pred prácou, na obed a večer, na konci pracovného dňa. Okrem toho ich podniky zaviedli špeciálne označovanie oblastí, ktoré im umožňujú sledovať poriadok vo výrobe, teda oblasti hotových výrobkov, skladovanie určitých dielov a pod. sú označené rôznymi farbami.
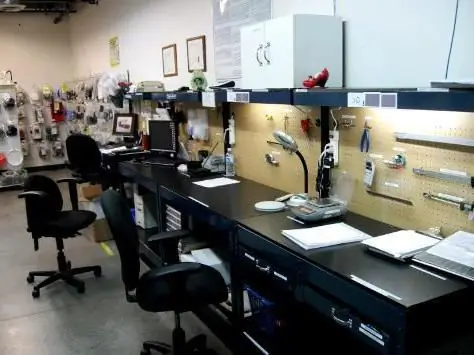
Štandardizácia
Princípy štandardizácie vynašiel Taiichi Ohno. Široko ich využíva aj moderný systém 5S. Riadenie výroby vďaka štandardizácii dostáva úžasný nástroj na kontrolu všetkých procesov. V dôsledku toho sa rýchlo odstránia príčiny oneskorení z harmonogramu a opravia sa chyby, ktoré vedú k uvoľneniu produktov nízkej kvality. V závode Toyota Motor vyzerala štandardizácia takto: majstri zostavovali denné plány práce, na pracovisku boli vyvesené presné pokyny a na konci pracovného dňa špeciálni pracovníci kontrolovali, ktoré odchýlky od plánu sa počas dňa vyskytli a prečo. Toto je základné pravidlo štandardizácie, teda presné pokyny, plány práce a kontrola ich plnenia. Teraz mnohé podniky, napríklad závody ENSTO v Estónsku, zavádzajú systém bonusov pre zamestnancov, ktorí prísne dodržiavajú ustanovenia systému 5C a na základe toho zvyšujú svoju produktivitu,je veľkou motiváciou prijať tento systém ako spôsob života.
Zlepšenie
Piaty krok, ktorým sa dokončuje systém „5S“vo výrobe, je založený na koncepte kaizen. Znamená to, že všetci zamestnanci bez ohľadu na svoju pozíciu by sa mali snažiť zlepšovať proces práce v oblasti, ktorá im bola zverená. Filozofickou podstatou kaizenu je, že celý náš život sa každým dňom zlepšuje, a keďže práca je súčasťou života, ani ona by nemala zostať bokom od zlepšení.
Pole pôsobnosti je tu široké, pretože dokonalosť nemá hraníc. Podľa konceptov Japoncov by samotní pracovníci mali chcieť zlepšiť svoj výrobný proces, bez pokynov alebo nátlaku. Teraz mnohé organizácie budujú tímy pracovníkov, ktorí monitorujú kvalitu produktov, učia ostatných o svojich pozitívnych skúsenostiach a pomáhajú dosahovať dokonalosť.
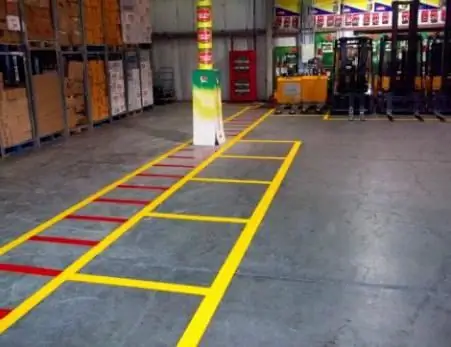
Základné chyby
Na to, aby systém „5C“začal fungovať, nestačí ho zorganizovať alebo najať zamestnancov, ktorí donútia svojich kolegov, aby ho zaviedli. Je dôležité, aby si ľudia uvedomili užitočnosť tejto inovácie a prijali ju ako životný štýl. Zavedenie systému „5S“v Rusku do výroby naráža na ťažkosti práve preto, že naša ruská mentalita je iná ako japonská. Mnohé z našich produkcií sa vyznačujú nasledujúcimi charakteristikami:
1. Zamestnanci, najmä ak pre nich neexistujú žiadne stimuly, sa nesnažia zvyšovať zisky podniku. Pýtajú sa,prečo sa snažiť urobiť šéfa ešte bohatším, keď už má všetko.
2. Samotní lídri nemajú záujem o zavedenie systému „5S“, pretože v tom nevidia účelnosť.
3. Mnoho direktív „zhora“sa zvykne vykonávať len pre „kliešť“. V Japonsku je k ich práci úplne iný prístup. Napríklad ten istý Taiichi Ohno, ktorý predstavil systém „5S“, nemyslel na osobný zisk, ale na prospech spoločnosti, v ktorej bol len inžinierom.
4. V mnohých podnikoch je systém 5S násilne zavádzaný. Štíhla výroba, ktorá znamená elimináciu strát všetkého druhu (pracovný čas, suroviny, dobrí zamestnanci, motivácia a iné ukazovatele), nefunguje, pretože pracovníci sa na podvedomej úrovni začínajú brániť inováciám, čo v konečnom dôsledku znižuje všetko úsilie na nulu..
5. Manažéri implementujúci systém úplne nechápu jeho podstatu, čo spôsobuje zlyhania v zavedených výrobných procesoch.
6. Štandardizácia sa často rozvinie do byrokracie, dobrý skutok je prerastený pokynmi a nariadeniami, ktoré len prekážajú v práci.
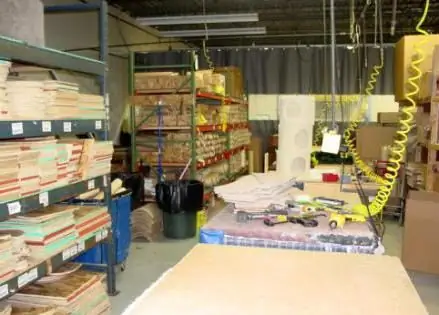
Recenzie
Rusi, ktorí zaviedli systém „5S“do výroby, spätná väzba na túto novinku je veľmi nejednoznačná. Vyzdvihnuté klady:
- lepšie byť na pracovisku;
- nerozptyľujte sa od práce zbytočnými maličkosťami;
- prehľadnejší pracovný postup;
- únava sa na konci zmeny znížila;
- mierne zvýšenéplat zvýšením produktivity práce;
- pokles pracovných úrazov.
Významné nevýhody:
- pri triedení nútia všetko vyhodiť;
- štandardizácia viedla k nárastu byrokracie;
- Zavedenie systému „5C“nezhoršilo problémy vo všetkých oblastiach podniku;
- Umiestnenie systému 5S na prvé miesto zatienilo dôležité problémy, ako je nedostatok náhradných dielov.
Odporúča:
Základné princípy požičiavania: popis, vlastnosti a požiadavky
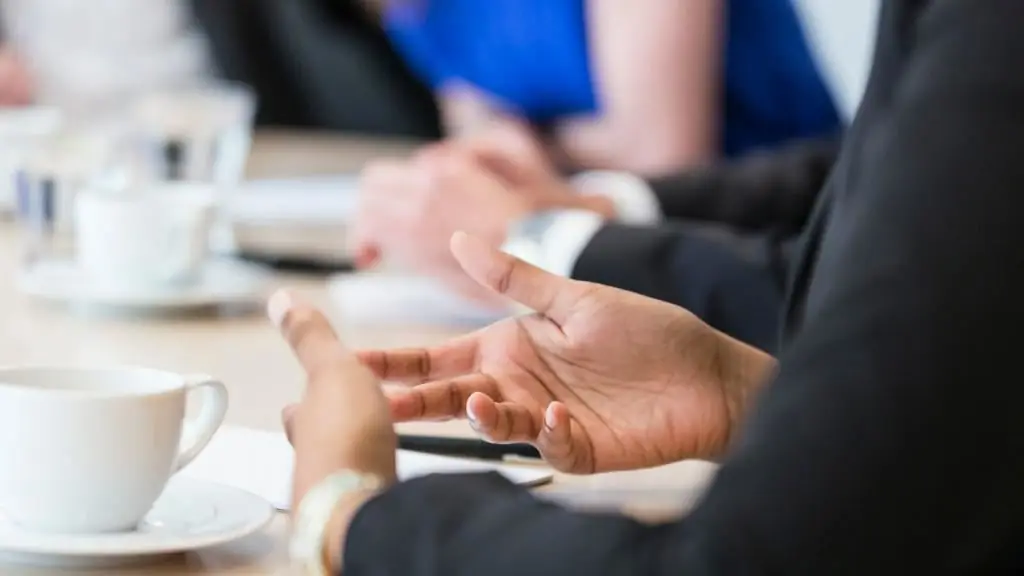
V našej ťažkej dobe ľudí často sužujú finančné problémy. Jedným z najlepších riešení v tejto situácii je pôžička. Zistite, aké sú zásady požičiavania a či spĺňate kritériá na vzorného dlžníka
Paradajky Gilgal F1: vlastnosti, popis odrody, pestovateľské vlastnosti, recenzie
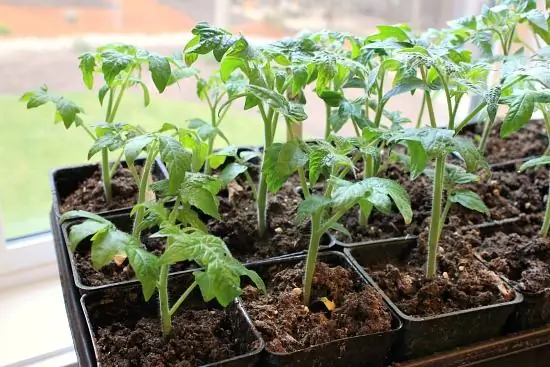
Paradajky Gilgal F1 si od záhradkárov vyslúžili dobré recenzie predovšetkým pre vynikajúcu chuť ovocia. Napriek tomu, že tieto paradajky sú hybridom prvej generácie, paradajky na nich dozrievajúce majú príjemnú vôňu a šťavnatú sladkokyslú dužinu
Tomato "Lady's man": recenzie, popis, vlastnosti, vlastnosti pestovania
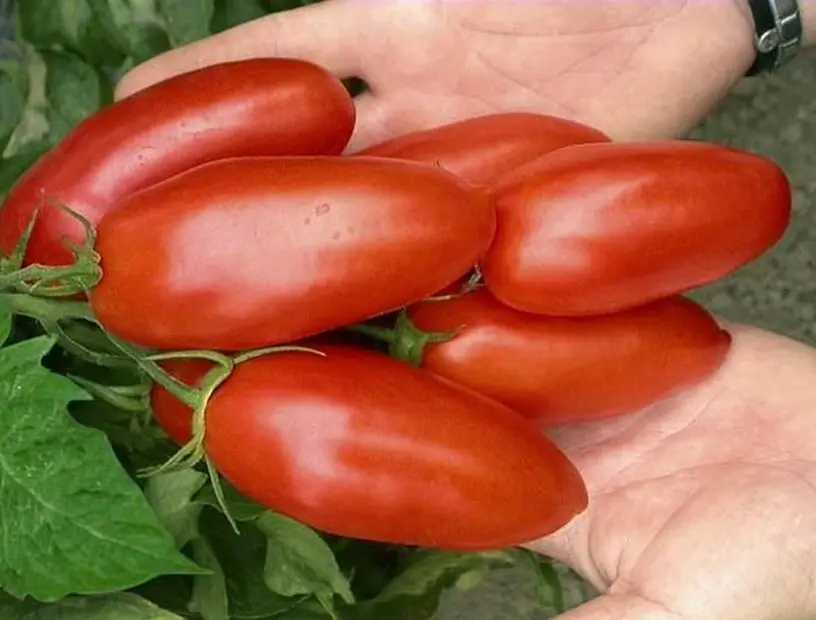
Odroda paradajok „Lady's Man“, ktorej recenzie sú mimoriadne pozitívne, je dnes lídrom medzi skoro dozrievajúcimi paradajkami. Amatérski záhradníci, ktorí aspoň raz sadili na svojich záhonoch, zostali vždy fanúšikmi."
Protilietadlový raketový systém. Protilietadlový raketový systém "Igla". Protilietadlový raketový systém "Osa"
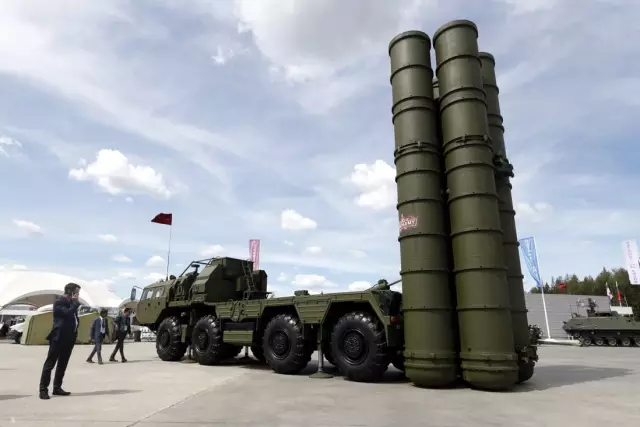
Potreba vytvorenia špecializovaných protilietadlových raketových systémov dozrela už počas druhej svetovej vojny, no vedci a zbrojári z rôznych krajín sa problematike začali podrobne venovať až v 50. rokoch. Faktom je, že dovtedy jednoducho neexistovali prostriedky na kontrolu protiraketových rakiet
Účtovníctvo vo výrobe a jeho vlastnosti
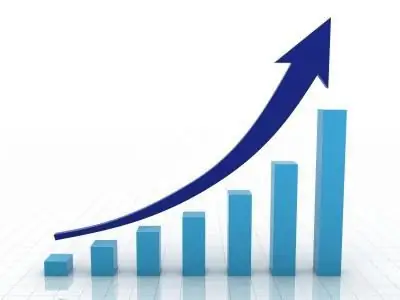
Účtovníctvo je najdôležitejším smerom práce výrobného podniku. Na základe akých princípov sa to dá realizovať? Aké sú hlavné úlohy účtovníctva vo výrobe?