2025 Autor: Howard Calhoun | [email protected]. Naposledy zmenené: 2025-01-24 13:24
V súčasnosti sa z ocele vyrába obrovské množstvo rôznych vecí, dielov atď.. To si samozrejme vyžaduje veľké množstvo východiskového materiálu. Preto sa v závodoch dlhodobo používa metóda kontinuálneho odlievania ocele, vyznačujúca sa najdôležitejšou vlastnosťou - vysokou produktivitou.
Základné vybavenie pre prácu
K dnešnému dňu je známych niekoľko zariadení na odlievanie ocele týmto spôsobom a sú označované skratkou UNRS. Spočiatku bola vyvinutá a uvedená do výroby inštalácia vertikálneho typu, ktorá sa nachádza 20-30 metrov pod úrovňou podlahy dielne. Neskôr sa však túžba opustiť prehĺbenie podlahy stala hlavným motorom rozvoja týchto inštalácií. To viedlo k vývoju a implementácii zariadení na kontinuálne odlievanie vežového typu. Výška týchto inštalácií bola 40 m. Táto verzia stroja však nebola široko používaná z dvoch dôvodov. Najprv postavtetakáto jednotka v dielni je dosť problematická a prácna. Po druhé, s jeho prevádzkou sa vyskytli ešte väčšie ťažkosti.
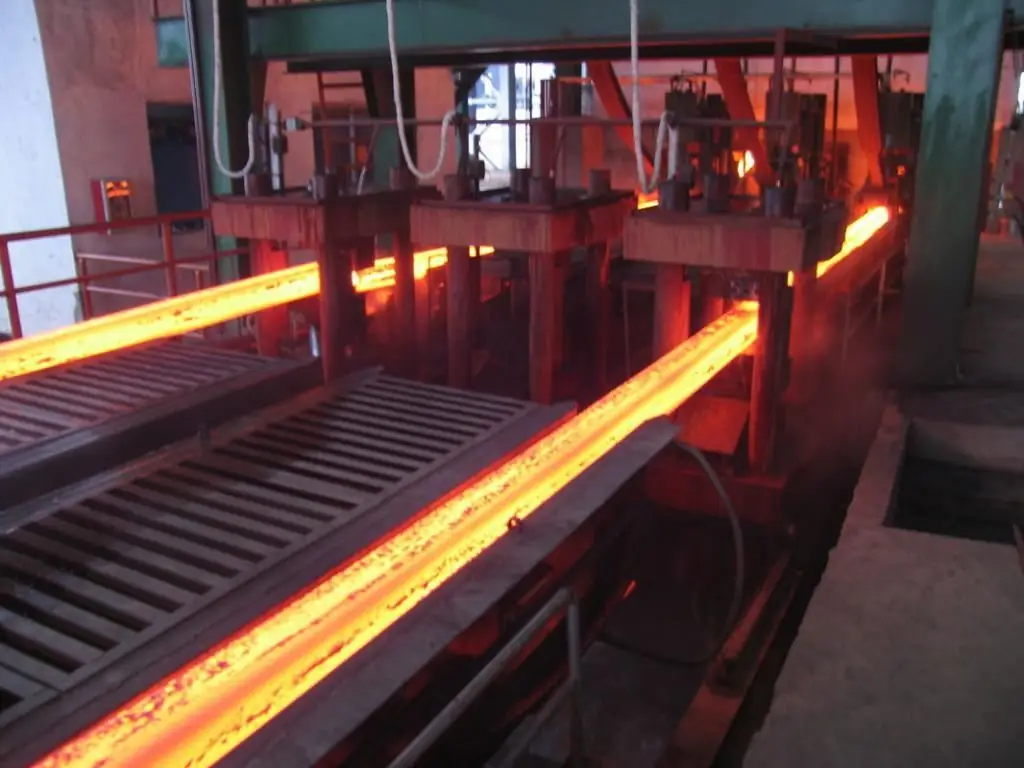
Zakrivené a radiálne inštalácie
Postupom času sa plynulé liatie ocele prenieslo na prácu s vertikálnymi ohýbacími strojmi. Hlavným znakom je ohyb ingotu vychádzajúceho za hriadeľmi o 90 stupňov. Potom sa v inštalácii použil špeciálny vyrovnávací mechanizmus na vyrovnanie ingotu a až po tejto fáze došlo k rezaniu. Kontinuálne odlievanie ocele na takýchto zariadeniach sa z nejakého dôvodu nestalo veľmi populárnym. Po prvé, ohyb samozrejme umožnil znížiť výšku, ale zároveň výrazne obmedzil prierez samotného ingotu. Čím viac bolo potrebné získať časť materiálu, tým väčší musel byť ohyb, čo znamená, že výška sa opäť zvýšila. Po druhé, ohýbacie stroje boli umiestnené v oceliarňach s ešte väčšími ťažkosťami ako vertikálne.
Zariadenia na plynulé odlievanie radiálnej ocele si dnes získavajú čoraz väčšiu obľubu. Na takejto jednotke sa ingot formuje vo forme a opúšťa ju pozdĺž rovnakého oblúka, pozdĺž ktorého do nej vstúpil. Potom sa narovná mechanizmom správneho ťahu. A potom už môžete začať rezať ingot na polotovary. Práve tento dizajn sa v praxi ukázal ako najracionálnejší pri organizovaní toku tovaru v oceliarni.
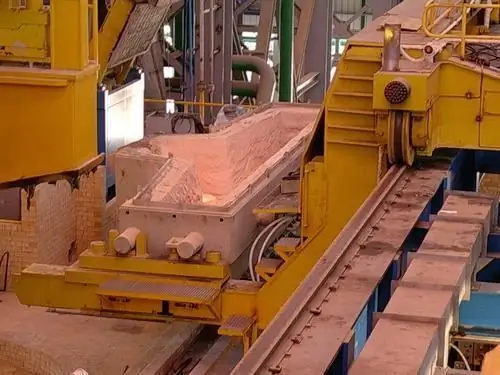
Kde sa začína odovzdávanie?
Technológia kontinuálneho spracovaniaodlievanie ocele je pomerne komplikovaný proces. Treba však povedať, že princíp zostáva rovnaký bez ohľadu na použité výrobné nastavenie. Technológiu môžete zvážiť pomocou príkladu vertikálneho UNRS.
Stroj sa dodáva s naberačkou na liatie ocele cez špeciálny žeriav. Potom oceľ prúdi do medzipanvy, ktorá má zátku. Pre jednovláknové stroje bude jedna zátka, pre viacvláknové stroje bude jedna zátka na prúd. Okrem toho má medzipanva špeciálnu priehradku na zachytenie trosky. Z medzipanvy bude oceľ prúdiť do formy, pričom prechádza cez dávkovacie sklo alebo zátku. Tu je dôležité poznamenať, že pred prvým odlievaním sa osivo vkladá do formy zo spodnej strany. Vypĺňa buď prierez celej formy, alebo len tvar obrobku. Horná vrstva semena bude dnom formy. Navyše má aj tvar lastovičieho chvosta pre budúce zapriahnutie ingotom.
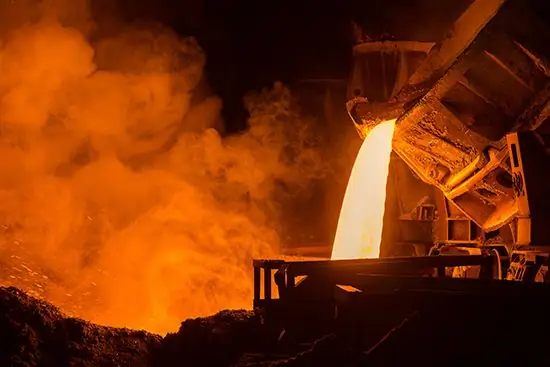
Ďalší casting
V procese kontinuálneho odlievania ocele je potrebné počkať, kým hladina surovín vystúpi nad osivo do výšky cca 300-400 mm. Keď k tomu dôjde, spustí sa mechanizmus, ktorý uvedie do činnosti ťažné zariadenie. Má ťahacie valce, pod vplyvom ktorých semienko spadne a stiahne so sebou aj vytvorený ingot.
Stroj na plynulé odlievanie má formu zvyčajne vyrobenú z medi s dutými stenami. Je pod napätímpôsobením chladiacej vody a jeho vnútorný prierez zodpovedá tvaru ingotu, ktorý sa má získať. Práve tu sa vytvára kôra ingotu. Pri vysokých rýchlostiach odlievania môže dôjsť k roztrhnutiu tejto kôry a úniku kovu. Aby sa tomu zabránilo, forma sa vyznačuje vratnými pohybmi.
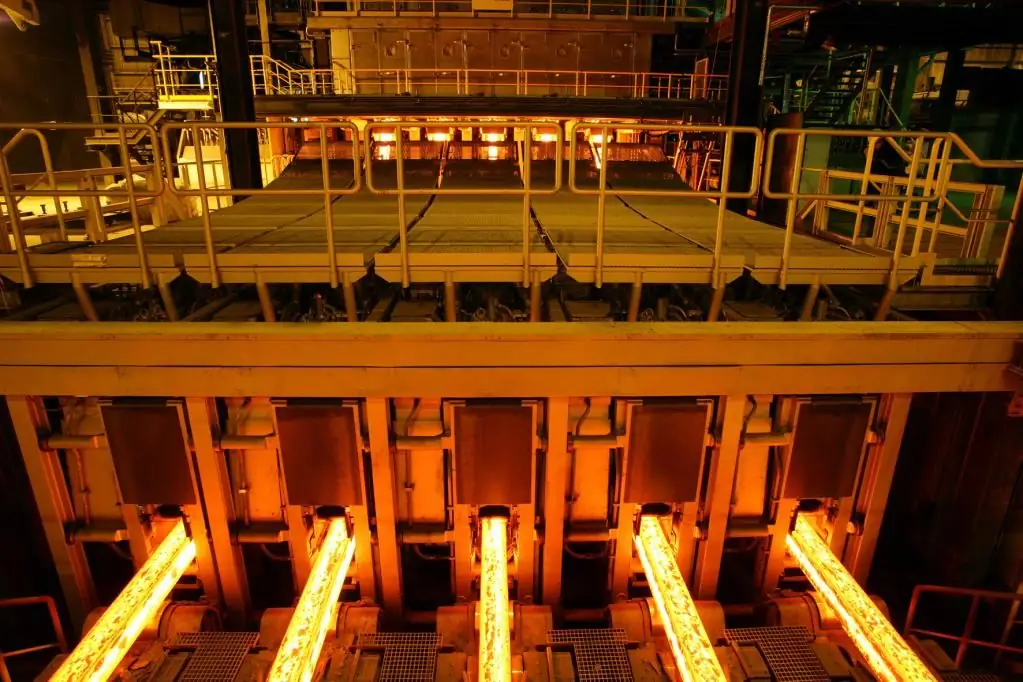
Charakteristiky prevádzky formy
Stroj na plynulé odlievanie má elektrický motor zodpovedný za vytvorenie tohto vratného pohybu. To sa deje prostredníctvom sily prevodovky s vačkovým výkyvným mechanizmom. Najprv sa forma pohybuje rovnakým smerom ako obrobok, teda dole, a po dokončení procesu sa vráti späť hore. Zdvih výkyvu je od 10 do 40 mm. Forma je dôležitým oddelením pri kontinuálnom odlievaní ocele na akomkoľvek type zariadenia, a preto sú jej steny mazané parafínom alebo akýmkoľvek iným mazivom vhodným pre danú charakteristiku.
Za zmienku stojí, že v moderných zariadeniach sa hladina kovu kontroluje rádiometricky privedením riadiaceho signálu na zátku naberačky. V samotnej forme môže byť nad úrovňou kovu vytvorená buď neutrálna alebo redukčná atmosféra, aby sa zabránilo oxidácii produktu počas výroby.
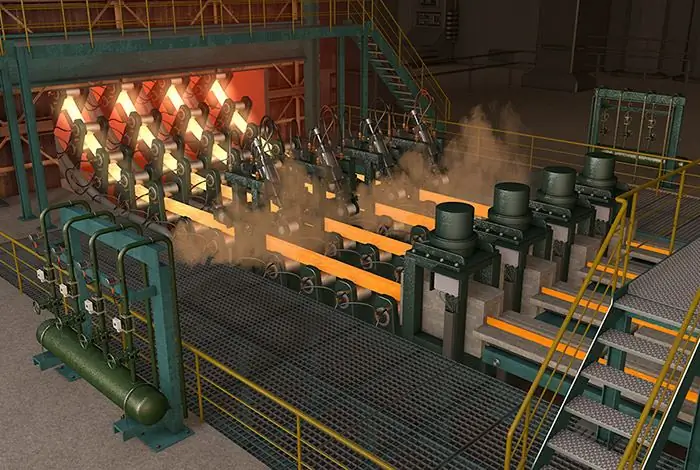
Šupka ingotu
Za zmienku stojí, že práca vo vákuu sa tiež považuje za sľubnú metódu odlievania. Jedna jednotka môže vykonávaťnalievanie cez niekoľko foriem naraz. Počet streamov jednej inštalácie tak môže dosiahnuť až osem.
Funkcia chladiča studeného semena sa používa na vytvorenie spodnej časti šupky ingotu. Ingot opustí formu pod vplyvom osiva, ktoré sa vtiahne do sekundárnej chladiacej zóny (SCZ). V strede polotovaru bude oceľ stále v tekutom stave. Tu je dôležité poznamenať, že podľa požiadaviek technológie odlievania ocele musí byť hrúbka plášťa v čase výstupu z formy minimálne 25 mm. Na splnenie týchto požiadaviek je potrebné zvoliť správny prietok materiálu.
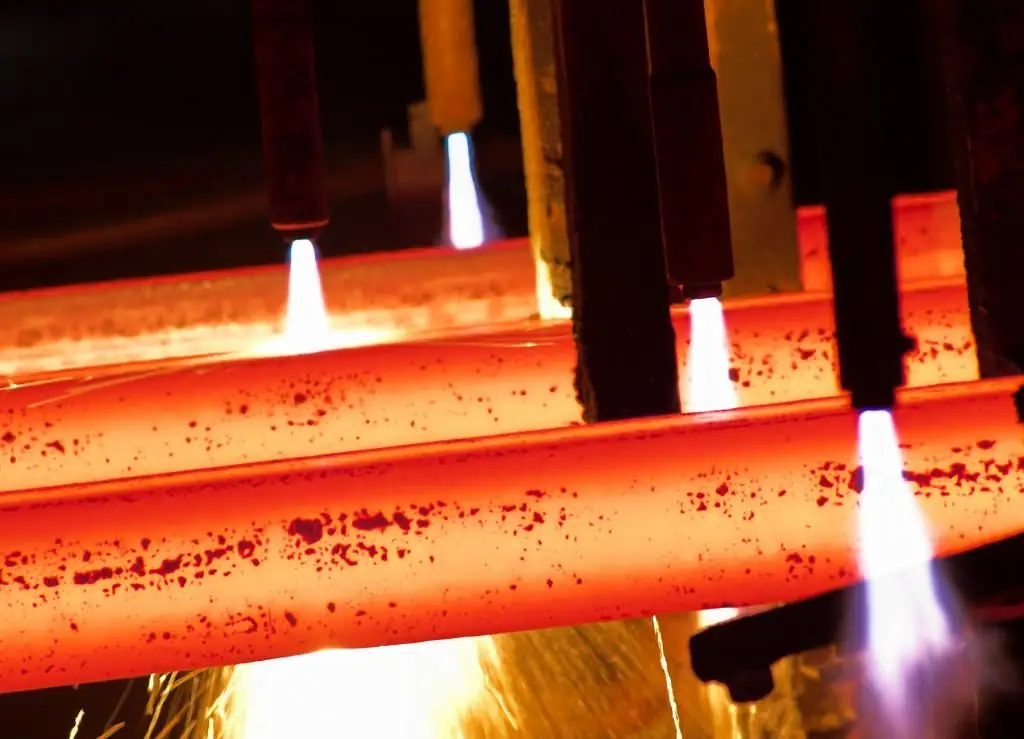
Charakteristiky procesu inštalácie a odlievania
Technologické charakteristiky sú približne nasledovné. Ak je prierez ingotu 160 x 900 mm, jeho rýchlosť by mala byť od 0,6 do 0,9 m / min. Ak je prierez 180x1000 mm, potom sa rýchlosť zníži na 0,55-0,85 m / min. Ukazovateľ najvyššej rýchlosti je potrebný pre prierez ingotu štvorcového typu 200x200 mm - 0,8-1,2 m/min.
Na základe vyššie uvedených ukazovateľov môžeme konštatovať, že priemerná rýchlosť odlievania jedného pásu technológiou kontinuálneho odlievania je 44,2 t/h. Ak prekročíte optimálnu rýchlosť, centrálna pórovitosť sa zvýši.
Ďalej stojí za zmienku, že stabilita odliatku a kvalita samotného výrobku sú ovplyvnené teplotou kovu. Empiricky sa zistilo, že pri teplote viac ako 1560 stCelzia Povrch ingotu je často pokrytý prasklinami. Ak je teplota nižšia, ako je uvedené, sklo bude často utiahnuté. Zistilo sa teda, že optimálna teplota pre metódu kontinuálneho odlievania ocele by bola 1540-1560 stupňov Celzia. Na udržanie tohto indikátora by teplota ohrevu pece pred uvoľnením mala byť v rozsahu 1630-1650 stupňov.
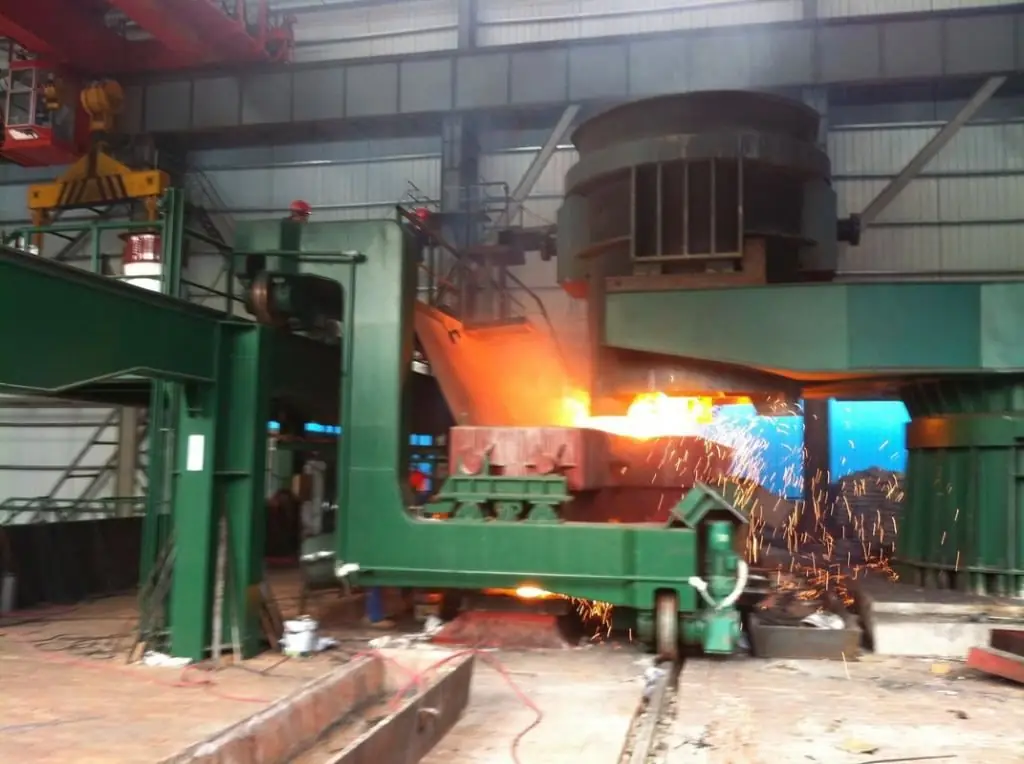
Sekundárna chladiaca zóna
V tejto sekcii sa najintenzívnejšie a priame chladenie ingotu realizuje pomocou vody pochádzajúcej zo spreja. Existuje špeciálny systém voľnobehu, nie výkonových valcov. Ich rotácia zabraňuje ohýbaniu alebo deformácii ingotu. V dôsledku intenzívneho chladenia v tejto zóne sa steny ingotu rýchlo zväčšia a kryštalizácia sa rozšíri do hĺbky. Rýchlosť ťahania ingotu a stupeň jeho ochladzovania by sa mal zvoliť tak, aby v čase, keď ingot vstúpi do ťahacích valcov, bol už úplne tuhý.
Aké sú výhody kontinuálneho liatia
Keďže tento spôsob odlievania ocele nahradil spôsob liatia do foriem, oplatí sa s týmto spôsobom porovnať. Vo všeobecnosti stojí za to zdôrazniť nasledujúce výhody: vyššia produktivita, znížené náklady a znížená pracovná náročnosť procesu. V dôsledku neustáleho vytvárania ingotu sa zmršťovacia dutina prenáša na chvost, na rozdiel od kokíl, kde každý ingot mal svoju vlastnú dutinu. Z tohto dôvodu sa výrazne zvyšuje percento výťažku vhodného kovu. UNRS vám umožňuje získaťobrobok rôznych tvarov, od malého štvorca 40x40 mm až po obdĺžnik 250x1000 mm. Použitie strojov na plynulé liatie umožnilo úplne opustiť kovania. To výrazne znížilo náklady na výrobný proces, a tým aj cenu na trhu. Okrem toho sa zjednodušil proces metalurgického spracovania.
Chyby
Napriek možnosti vysokej mechanizácie a automatizácie procesu, vysokému percentu dobrých ingotov a iným výhodám opísaným vyššie má táto metóda aj niektoré negatívne stránky. Nevýhody plynulé liatie ocele sú nasledovné.
Po prvé, nie je možné vyrábať ingoty komplexnej konfigurácie. Po druhé, rozsah ingotov a prírezov je značne obmedzený. Je dosť ťažké prestavať stroje na nalievanie surovín inej značky, čo môže zvýšiť konečné náklady na produkt inej značky, ak sa vyrába v rovnakom závode. Niektoré druhy ocele, napríklad varné, sa touto metódou vôbec nedajú vyrobiť.
Posledná nevýhoda kontinuálneho spôsobu odlievania ocele je veľmi významná. Je to možná porucha zariadenia. Zlyhanie UNRS povedie k obrovským stratám výkonu. Čím dlhšie bude oprava trvať, tým väčšie straty porastú.
Odporúča:
Hustota ocele v kg/m3. Uhlíkové a legované ocele
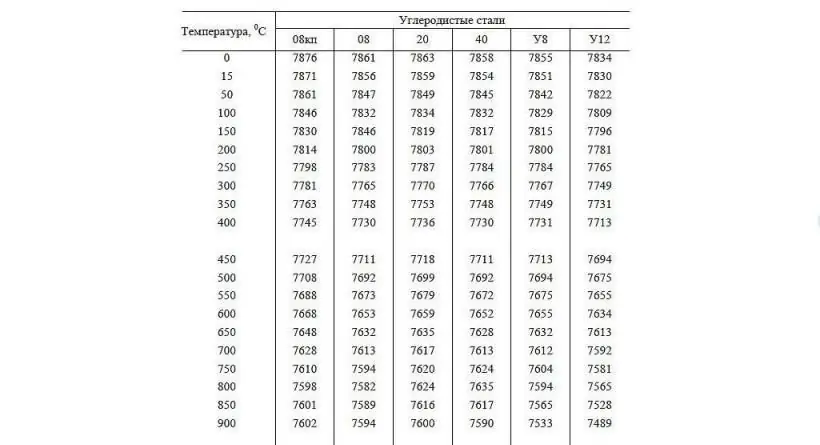
Ocel je najbežnejším kovovým materiálom v priemysle, na základe ktorého sa vyrábajú konštrukcie a nástroje s požadovanými vlastnosťami. V závislosti od účelu tohto materiálu sa menia mnohé jeho fyzikálne vlastnosti vrátane hustoty. V tomto článku zvážime, aká je hustota ocele v kg / m3
Gravírovanie do plexiskla: výhody a nevýhody, technológia, vybavenie
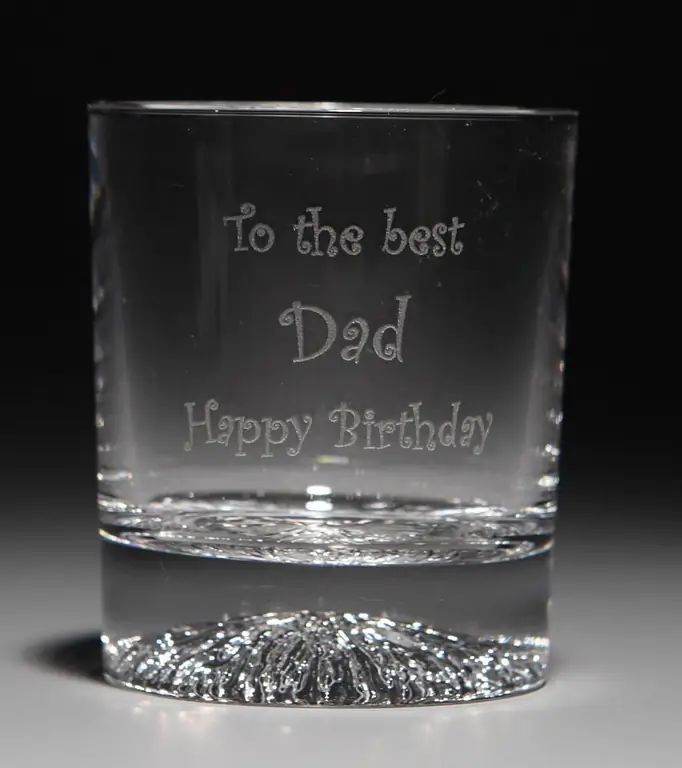
Gravírovanie do plexiskla sa považuje za maliarske remeslo. Suvenírová figúrka, vitráže alebo sklenený stolík, ktoré sú zdobené nádhernými kresbami, stelesňujú jemný umelecký vkus. Technológie morenia a pieskovania sú minulosťou. Dnes si pomocou laserového stroja môže každý človek vytvoriť veľmi detailný vzor
Kníhtlač je Technológia kníhtlače, moderné stupne vývoja, potrebné vybavenie, výhody a nevýhody tohto druhu tlače
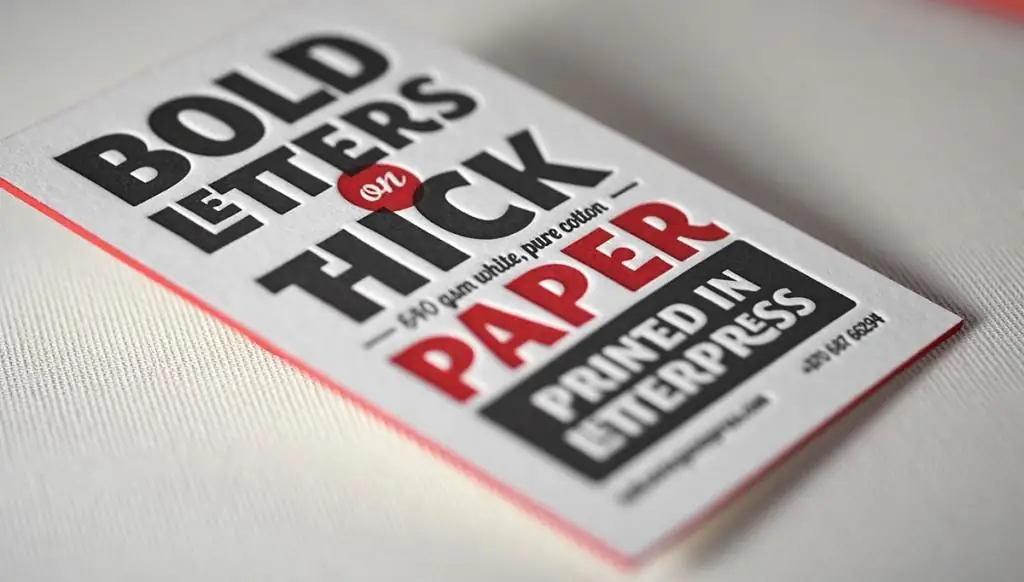
Knihtlač je jednou z typických metód aplikácie informácií pomocou reliéfnej matrice. Prvky, ktoré vyčnievajú, sú pokryté farbou vo forme pasty a potom pritlačené na papier. Takto sa replikujú rôzne masové periodiká, príručky, knihy a noviny
Odlievanie do silikónovej formy: vybavenie. Vákuové liatie do silikónových foriem
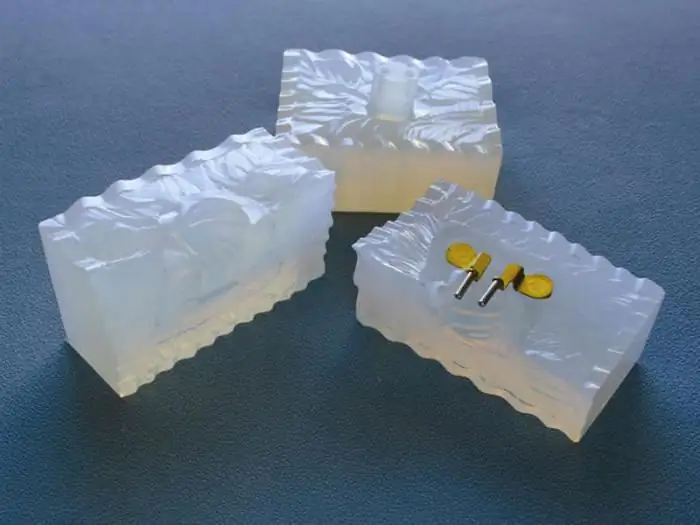
Na výrobu malého počtu plastových polotovarov sa najčastejšie používa vákuové liatie do silikónových foriem. Táto metóda je pomerne ekonomická (výroba kovovej formy vyžaduje viac času a peňazí). Silikónové formy sa navyše používajú opakovane a aj to výrazne znižuje náklady na výrobu
Princíp činnosti dieselového motora: vlastnosti, výhody a nevýhody
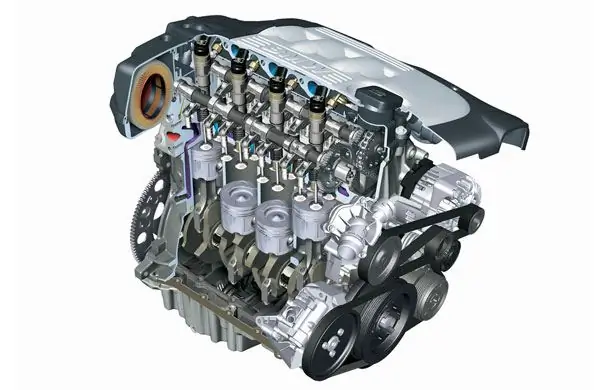
Naftové autá na našich cestách nie sú v žiadnom prípade nezvyčajné. V krajinách západnej Európy sú vo väčšine. Dieselové motory majú oproti benzínovým motorom množstvo výhod. Zároveň však existujú určité nevýhody. Čo je to za motor, aké je dieselové zariadenie a princíp činnosti? Zvážte to v našom dnešnom článku